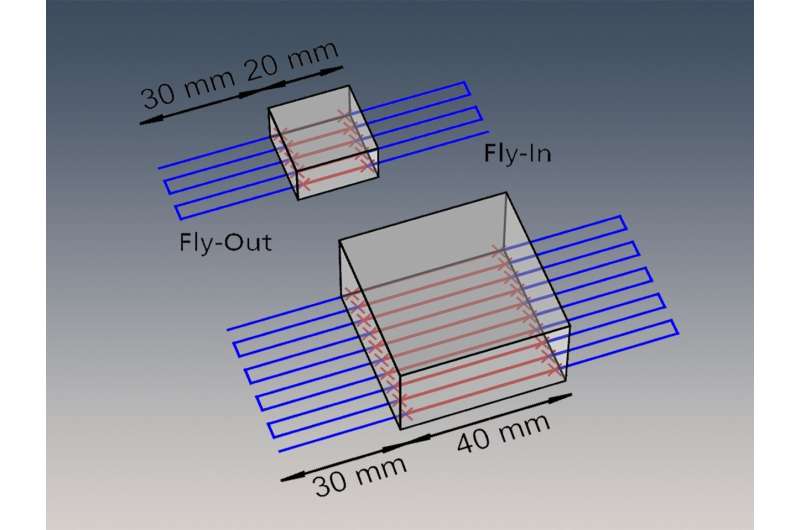
Alta dinámica: con EHLA 3D, la productividad se hunde y nada con la interacción de fly-in y fly-out. Crédito: Fraunhofer ILT, Aquisgrán, Alemania
¿Pueden los componentes metálicos sofisticados imprimirse en 3D de manera productiva y reproducible en serie? Investigadores de Aquisgrán pueden responder afirmativamente a esta pregunta: en el Instituto Fraunhofer de Tecnología Láser ILT, han transferido EHLA de deposición de material láser de alta velocidad extrema bidimensional a un sistema CNC modificado de cinco ejes para la fabricación aditiva de componentes complejos.
Al extender el proceso EHLA a la tercera dimensión, el instituto puede imprimir en 3D materiales difíciles de soldar, como aceros para herramientas, titanio, aluminio y aleaciones a base de níquel.
Durante décadas, dos procesos láser han dominado la impresión y el recubrimiento de componentes metálicos. La tecnología dominante en la impresión 3D metálica industrial directa es el proceso de fusión de lecho de polvo basado en láser (LPBF) patentado por Fraunhofer ILT hace 26 años. Aquí, la radiación láser funde una pequeña parte del material base y convierte el polvo en una capa sólida que se adhiere metalúrgicamente al material base. De esta manera, un componente 3D crece capa por capa a partir del lecho de polvo.
La deposición de material por láser (LMD) también ha demostrado ser una tecnología de superficie eficiente de un tipo especial. En LMD, se forma un baño de fusión en la superficie del componente, en el que se introduce continuamente el material de relleno, alambre o polvo. Esta piscina funde tanto el sustrato como el material de relleno, lo que da como resultado una unión metalúrgica entre la capa y el sustrato del componente.
Recuperación de componentes caros
El potencial económico radica, por un lado, en la posibilidad de actualizar los componentes básicos con una capa funcional o realizar modificaciones locales aditivas de los componentes. La segunda área importante de aplicación de LMD es la reparación, es decir, la recuperación de componentes costosos, por ejemplo, de la industria aeroespacial o la fabricación de herramientas. Los componentes desgastados o defectuosos pueden volver a funcionar completamente después del revestimiento local con LMD y, por lo tanto, ya no tienen que desecharse.
LMD y LPBF se han vuelto indispensables para la fabricación aditiva basada en metal, ya que tienen ventajas específicas del proceso: LMD es atractivo gracias a su alta productividad, mientras que LPBF se puede utilizar para la impresión 3D de componentes extremadamente complejos y de filigrana. Fraunhofer ILT y la Cátedra de Producción Aditiva Digital DAP en la Universidad RWTH de Aquisgrán abrieron un camino completamente nuevo en 2012 con el desarrollo de EHLA de deposición de material por láser de alta velocidad extrema.
En el proceso patentado, un láser funde las partículas de polvo que ya se encuentran por encima del baño de fusión. Gracias a esta innovación, la velocidad del proceso se pudo aumentar de los 0,5 a 2,0 (LMD) anteriores hasta 200 m/min y el espesor del recubrimiento se redujo de 500 a 10 µm. Ahora se pueden recubrir hasta cinco metros cuadrados por hora. Además, los recubrimientos se han vuelto más suaves, con una rugosidad reducida a una décima parte del valor típico para LMD.
Éxitos internacionales en recubrimiento rápido
La invención se ha puesto de moda: Hornet Laser Cladding BV de Lexmond (Países Bajos), por ejemplo, ha integrado una fuente de haz láser, un cabezal de procesamiento EHLA y un sistema de alimentación de polvo en sus tornos para utilizar EHLA en procesos industriales. TRUMPF Laser- und Systemtechnik GmbH, con sede en Ditzingen, Alemania, también incluyó el proceso en su cartera de productos y ofrece equipos láser y tecnologías de sistemas para el proceso EHLA.
Entre los primeros usuarios se encuentran empresas de los Países Bajos, China, Alemania y Turquía. El gran avance se produjo en 2015 para el sector offshore: desde entonces, muchos cientos de cilindros hidráulicos de metros de largo se han revestido con aleaciones resistentes al desgaste y la corrosión para su uso en todo el mundo en entornos marítimos.
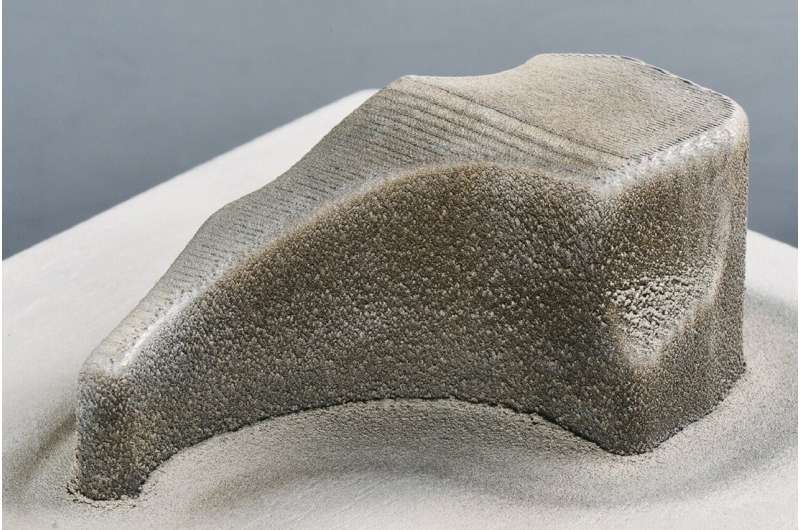
Rápido y preciso: utilizando el ejemplo de una pieza moldeada fabricada de forma aditiva con EHLA 3D, el instituto demostró que podía reducir significativamente el tiempo de impresión en comparación con LMD y LPBF. Crédito: Fraunhofer ILT, Aquisgrán, Alemania.
En 2019, el paso a la tercera dimensión siguió a otros éxitos en el recubrimiento rápido y fiable de discos de freno, pistones, cilindros y cojinetes. Jonathan Schaible, ex investigador asociado de Fraunhofer ILT, participó en el desarrollo posterior como parte de su doctorado: abordó la cuestión de qué requisitos especiales para la tecnología de máquinas y sistemas deben cumplirse para combinar EHLA con impresión 3D de alta velocidad.
Paralelamente, su sucesor, Min-Uh Ko, ha seguido perfeccionando la ingeniería de procesos en un sistema CNC de cinco ejes especialmente modificado que combina la máxima precisión con altas tasas de avance para la fabricación aditiva, el recubrimiento de forma libre y la reparación de componentes mediante EHLA.
«EHLA 3D combina la productividad de LMD con sus capas de 500 a 2000 µm de espesor con la acumulación precisa y estructuralmente específica de LPBF con capas de 30 a 100 µm de espesor», explica Min-Uh Ko, líder del grupo de fabricación aditiva y reparación LMD en el Instituto Fraunhofer de Tecnología Láser ILT. «EHLA 3D está en el rango medio con 50 a 300 µm».
Cerca del contorno final
La zona de baja dilución y la alta velocidad de enfriamiento también hablan a favor del proceso. Gracias a estas propiedades, los componentes hechos de materiales que son difíciles de soldar y los emparejamientos de múltiples materiales también se pueden producir de forma aditiva. El proceso muestra sus puntos fuertes en la impresión 3D real.
El científico Ko explica: «Con EHLA 3D, es posible fabricar de forma productiva componentes que ya se acercan mucho al contorno final. Además de la llamada conformación casi neta, el proceso también permite construir de forma rápida y precisa, como así como aplicar revestimientos en superficies de forma libre».
Formas complejas en un tiempo récord: esto solo es posible con una tecnología de máquina diseñada apropiadamente y una planificación de ruta adaptada de los programas CNC. La productividad se hunde o nada aquí a medida que el llamado fly-in, cuando el cabezal del láser acelera hasta el punto de uso con el rayo láser encendido, interactúa con el fly-out subsiguiente, cuando desacelera fuera de la zona de procesamiento.
La eficiencia resulta de la relación entre el tiempo de procesamiento con el rayo láser encendido y el tiempo total del proceso. Las investigaciones de Schaible lo demuestran: con una aceleración de 50 m/s² y una velocidad de avance de 50 m/min para una distancia de 100 mm, la eficiencia M-PDE (eficiencia de deposición de polvo relacionada con la máquina) es de alrededor del 80 por ciento. Con una aceleración de 10 m/s², la M-PDE es de aprox. 40 por ciento
El esfuerzo del instituto para desarrollar aún más el proceso EHLA ha valido la pena, como lo demostró una mirada a las primeras demostraciones exitosas. En el «AKL’22—Congreso Internacional de Tecnología Láser» en Aquisgrán, Alemania, el científico Ko mostró el progreso actual de la tecnología EHLA 3D durante su presentación en la primavera de 2022.
Por ejemplo, un video demostró la fabricación aditiva productiva de una herramienta de formación cuyo tiempo de impresión podría reducirse a la mitad en comparación con LMD. Además, otras ventajas resultan de la reducción en el esfuerzo requerido para el mecanizado de acabado.
Impresión 3D de metal fiable con polvo usado
El proceso también se caracteriza por su alta eficiencia: los componentes fabricados con el material aeroespacial Inconel 718 se imprimieron en 3D en el sistema CNC de cinco ejes a una tasa de deposición de más de 2 kg/h con una densidad superior al 99,5 %. Los investigadores de Aquisgrán también investigaron cómo cambian los valores característicos cuando trabajan con polvo de metal reciclado en lugar de nuevo. En ambos casos, la resistencia a la tracción Rm fue de alrededor de 1300 MPa.
Ko explica: «En ambos casos, la resistencia a la tracción resultó ser tan buena como con la fundición». También obtuvo buenos resultados el científico Schaible, cuyo trabajo incluyó el desarrollo del proceso EHLA 3D de componentes hechos de acero inoxidable 316L y aleaciones de aluminio y silicio. Aquí, también, las propiedades mecánicas obtenidas están en línea con las reportadas en la literatura para muestras producidas convencionalmente. La resolución estructural actualmente posible de los componentes de aluminio de pared delgada producidos con EHLA 3D es de alrededor de 500 µm.
El sistema CNC ubicado en Fraunhofer ILT es un prototipo especialmente adaptado que puede mover la herramienta de manera confiable, precisa y al mismo tiempo altamente dinámica. Ko invita a las partes interesadas a mirar un poco más de cerca: «Si está interesado en esta tecnología de planta u otros posibles usos para el proceso EHLA 3D, estaré encantado de ayudarle aquí en Fraunhofer ILT».
Más información:
Conferencia: www.ilt.fraunhofer.de/en/ferias … 2022/laser-2022.html
Citación: Expansión de la deposición de material láser de alta velocidad extrema a la tercera dimensión (2 de febrero de 2023) consultado el 2 de febrero de 2023 en https://techxplore.com/news/2023-02-extreme-high-speed-laser-material-deposition. html
Este documento está sujeto a derechos de autor. Aparte de cualquier trato justo con fines de estudio o investigación privados, ninguna parte puede reproducirse sin el permiso por escrito. El contenido se proporciona únicamente con fines informativos.